When it comes to the choice of materials used in motorcycle helmet shells, does your helmet truly offer the protection needed?
With a range of materials like Polycarbonate, Fiberglass composite, Carbon Fiber, and Multi-Composite, each option brings unique attributes that affect safety, weight, and comfort on the road.
Understanding these choices is not just about picking a helmet but about elevating your riding experience and confidence. Dive into the specifics as we explore the fundamental components that shape the helmet and the protection it provides.
Understanding the Materials in Motorcycle Helmet Shells
The choice of materials in motorcycle helmet shells plays a critical role in both safety and performance. The shell is the first line of defense in an impact, designed to absorb and distribute energy effectively to minimize head injuries.
Advanced materials such as Polycarbonate, Fiberglass Composite, Carbon Fiber, and Multi-Composite are used to craft helmets that cater to different riding styles and needs. Each material contributes uniquely to the helmet's ability to safeguard the rider while maintaining a balance between weight and aerodynamics.
These materials not only enhance the protective capabilities but also influence the overall feel, making helmets more comfortable for extended use.
-
Polycarbonate
-
Fiberglass Composite
-
Carbon Fiber
- Multi-Composite
Polycarbonate is known for its durability and impact absorption, making it a popular choice despite its heavier weight. Fiberglass Composite offers a lighter alternative, effectively dispersing impact energy, though it often comes at a higher price.
Carbon Fiber, renowned for its high strength-to-weight ratio, provides superior protection and comfort, ideal for those who prioritize lightweight helmets. Multi-Composite shells integrate various materials to optimize these features, offering a comprehensive solution that balances protection, weight, and comfort.
The careful selection and combination of these materials ensure that helmets not only meet safety standards but also offer enhanced comfort and reduced fatigue during rides.
Exploring Polycarbonate Helmet Shells
Polycarbonate helmets are renowned for their robust durability and impressive impact resistance. When a rider faces an accident, these helmets excel at absorbing impact energy, reducing the risk of head injuries.
This ability to disperse energy efficiently makes polycarbonate a favored choice among riders seeking reliable protection. Its inherent toughness ensures that the helmet can withstand the rigors of daily use, maintaining its structural integrity over time.
Despite its benefits, polycarbonate helmets come with certain drawbacks. The material's density contributes to a heavier helmet, which can lead to increased neck fatigue during long rides.
Additionally, polycarbonate is less resistant to scratches than other materials, potentially affecting the helmet's appearance and clarity over time. While these factors may deter some riders, the balance of safety and cost-effectiveness continues to make polycarbonate a popular option in the world of motorcycle helmets.
The Advantages of Fiberglass Composite Helmet Shells
Fiberglass composite helmet shells excel in distributing impact energy, which is a critical feature for reducing the risk of injuries during a crash. When a helmet encounters an impact, the fiberglass construction efficiently spreads the force across the shell's surface, minimizing the pressure transmitted to the rider's head.
This energy distribution capability makes fiberglass helmets a preferred choice for those prioritizing safety. Additionally, fiberglass shells are lighter than their polycarbonate counterparts, offering riders reduced neck fatigue and enhanced comfort during long rides. The lightweight nature of fiberglass contributes to a more enjoyable riding experience without compromising protection.
The production of fiberglass composite helmets involves a more intricate and labor-intensive process, which often results in a higher price point. This process includes layering glass fibers with epoxy resins, which requires precision and care to achieve the optimal balance of strength and weight.
Despite the increased cost, many riders find the investment worthwhile due to the superior protection and comfort provided by fiberglass helmets.
In terms of helmet design and technology, fiberglass composites offer significant advantages. The flexibility in layering allows manufacturers to create intricate designs and shapes, enhancing both the aerodynamics and aesthetics of the helmet.
This adaptability in design leads to advancements in helmet technology, enabling the integration of features such as improved ventilation systems and enhanced noise reduction. Overall, fiberglass composite shells not only provide robust protection but also contribute to the evolution of helmet design and technology, meeting the demands of modern riders.
The Premium Qualities of Carbon Fiber Helmets
Carbon fiber helmets are celebrated for their exceptional lightweight and durable attributes, making them a top choice for riders who prioritize both safety and comfort. The material's high strength-to-weight ratio is achieved through its crystalline molecular structure, which allows the helmet to offer superior protection without the bulk.
This lightweight nature significantly reduces neck strain, especially during long rides, enhancing the overall riding experience. Furthermore, carbon fiber's durability ensures that the helmet can withstand substantial impacts while maintaining its integrity, providing reliable head protection in the event of an accident.
As a result, these helmets are often favored by professional racers and avid motorcyclists who seek top-tier performance and safety.
Although carbon fiber helmets offer remarkable benefits, they come with a higher price tag due to the advanced technology and materials involved in their production. The manufacturing process for carbon fiber involves layering multiple sheets of carbon filaments with epoxy resins, requiring precision and state-of-the-art equipment.
This complexity not only contributes to the strength and lightweight properties of the helmet but also drives up the cost. Despite the financial investment, many riders consider the enhanced protection and comfort provided by carbon fiber helmets to be well worth the expense, ensuring peace of mind on the road.
Material | Weight | Cost |
---|---|---|
Polycarbonate | Heavy | Low |
Fiberglass | Medium | Medium |
Carbon Fiber | Light | High |
Multi-Composite | Medium | Medium |
The Versatility of Multi-Composite Helmet Shells
What are motorcycle helmet shells made of? Multi-composite shells are crafted by combining various materials to maximize protection while maintaining comfort and a lightweight profile. These shells often integrate components such as polycarbonate, fiberglass, and occasionally carbon fiber.
This blend allows the helmet to harness the unique characteristics of each material, resulting in a shell that effectively absorbs impacts, remains durable, and is lightweight enough to reduce rider fatigue.
-
Enhanced protection
-
Balanced weight
-
Improved comfort
In modern helmet manufacturing, multi-composite shells play a pivotal role by leveraging advanced materials and engineering techniques. Manufacturers can tailor the properties of each layer within the shell, achieving a synergy of strength and flexibility.
This results in helmets that not only meet stringent safety standards but also cater to the varying needs of riders. The ability to fine-tune the composite layers allows for innovative designs that enhance aerodynamics, ventilation, and overall rider experience. This adaptability makes multi-composite helmets a popular choice for those seeking a harmonious blend of safety and performance.
Understanding Helmet Safety Standards and Certifications
Helmet safety standards are pivotal in ensuring that motorcycle helmets provide adequate protection during impacts. These standards, such as DOT, ECE, and SNELL, serve as benchmarks for evaluating a helmet's capability to safeguard riders.
They encompass a range of tests that assess impact resistance, penetration resistance, and retention system effectiveness. By adhering to these standards, manufacturers can guarantee that their helmets offer the necessary protection to prevent head injuries.
For riders, choosing a helmet that meets these certifications is crucial, as it directly impacts their safety on the road. Moreover, the presence of these standards aids in maintaining consistent quality across helmet models, providing riders with confidence in their gear.
DOT Certification
The Department of Transportation (DOT) certification is mandatory for all helmets sold in the United States. This standard focuses on three primary testing criteria: impact attenuation, penetration resistance, and the effectiveness of the retention system.
Helmets must demonstrate the ability to absorb and disperse energy from impacts, ensuring that the force transmitted to the rider's head is minimized. DOT-certified helmets undergo rigorous testing to confirm their structural integrity and the reliability of their chin straps, ensuring they remain securely fastened during a crash.
By meeting DOT requirements, helmets provide a baseline level of protection deemed necessary for safe riding on U.S. roads.
ECE Certification
The Economic Commission for Europe (ECE) certification is recognized globally, with many countries adopting it as their standard for helmet safety. Unlike DOT, ECE standards involve more comprehensive testing procedures, including assessments of shell rigidity and optical quality of visors.
ECE-certified helmets are subjected to additional evaluations, such as environmental conditioning tests, to ensure they maintain performance under various conditions. This global recognition allows ECE-certified helmets to be trusted worldwide, making them an appealing choice for riders who travel internationally.
The widespread acceptance of ECE standards underscores their importance in promoting helmet safety across borders.
For riders, understanding and selecting helmets that meet established safety standards is paramount. These certifications not only provide peace of mind but also ensure that the helmet has been tested against stringent criteria to offer the best possible protection.
Whether opting for DOT, ECE, or SNELL-certified helmets, riders can be confident that their headgear is crafted to withstand the demands of the road, ultimately contributing to a safer riding experience.
Future Trends in Motorcycle Helmet Materials
Innovative designs in helmet materials are at the forefront of industry trends, with ongoing advancements transforming the landscape of helmet technology. Currently, materials like graphene and advanced polymers are being explored to enhance strength and reduce weight even further than traditional options.
These innovations promise to improve not only the protective capabilities of helmets but also the comfort levels, making them more adaptable to various riding conditions. The integration of smart technology into helmet materials is another exciting development, providing features such as impact sensors and communication systems for riders.
Looking ahead, the potential future developments in helmet materials are expected to significantly impact safety and performance. Researchers are investigating the use of nanotechnology to create helmets that can better withstand multiple impacts without compromising the shell's integrity.
Additionally, eco-friendly materials are being considered to reduce the environmental impact of helmet production. These advancements are set to redefine the standards of rider safety, offering enhanced protection and comfort while maintaining a focus on sustainability.
Final Words
Choosing the right helmet starts with understanding what are motorcycle helmet shells made of. The materials—Polycarbonate, Fiberglass composite, Carbon Fiber, and Multi-Composite—impact protection, comfort, and weight.
Polycarbonate offers reliable impact absorption, while Fiberglass is lighter with advanced design benefits. Carbon fiber excels in lightweight durability, and Multi-Composite combines multiple advantages.
Awareness of ongoing trends and safety standards ensures you select a helmet that maximizes both protection and riding enjoyment.
FAQ
Q: What are motorcycle helmet shells made of?
A: Motorcycle helmet shells are typically made from polycarbonate, fiberglass composite, carbon fiber, and multi-composite materials. Each material offers unique advantages concerning safety, weight, and comfort.
Q: What is the best material for a motorcycle helmet shell?
A: The best material for a motorcycle helmet shell varies based on needs; carbon fiber offers superior protection and lightweight construction, while being more costly. Fiberglass provides a balance of cost and performance.
Q: What are the properties of carbon fiber helmets?
A: Carbon fiber helmets are known for their exceptional durability and lightweight nature, providing premium protection. They are, however, more expensive compared to other helmet materials.
Q: What materials are used in motorcycle helmet liners?
A: Motorcycle helmet liners are typically made from expanded polystyrene (EPS), designed to absorb impact energy and provide cushioning during a crash.
Q: How do fiberglass composite helmets benefit riders?
A: Fiberglass composite helmets effectively distribute impact energy and tend to be lighter than polycarbonate helmets. Their complex production process makes them costlier, but they offer enhanced design and safety features.
Q: What is polycarbonate used for in helmets?
A: Polycarbonate is used in helmets for its durable nature and ability to absorb impact energy. Helmets made from it are heavier and less resistant to scratches.
Q: What are military helmets made of?
A: Military helmets are usually made from advanced composite materials, such as Kevlar and ballistic fibers, tailored for enhanced impact resistance and protection in combat scenarios.
Q: What are the advantages of multi-composite helmet shells?
A: Multi-composite helmet shells provide enhanced protection, balanced weight, and improved comfort by combining different materials like polycarbonate, fiberglass, and sometimes carbon fiber.
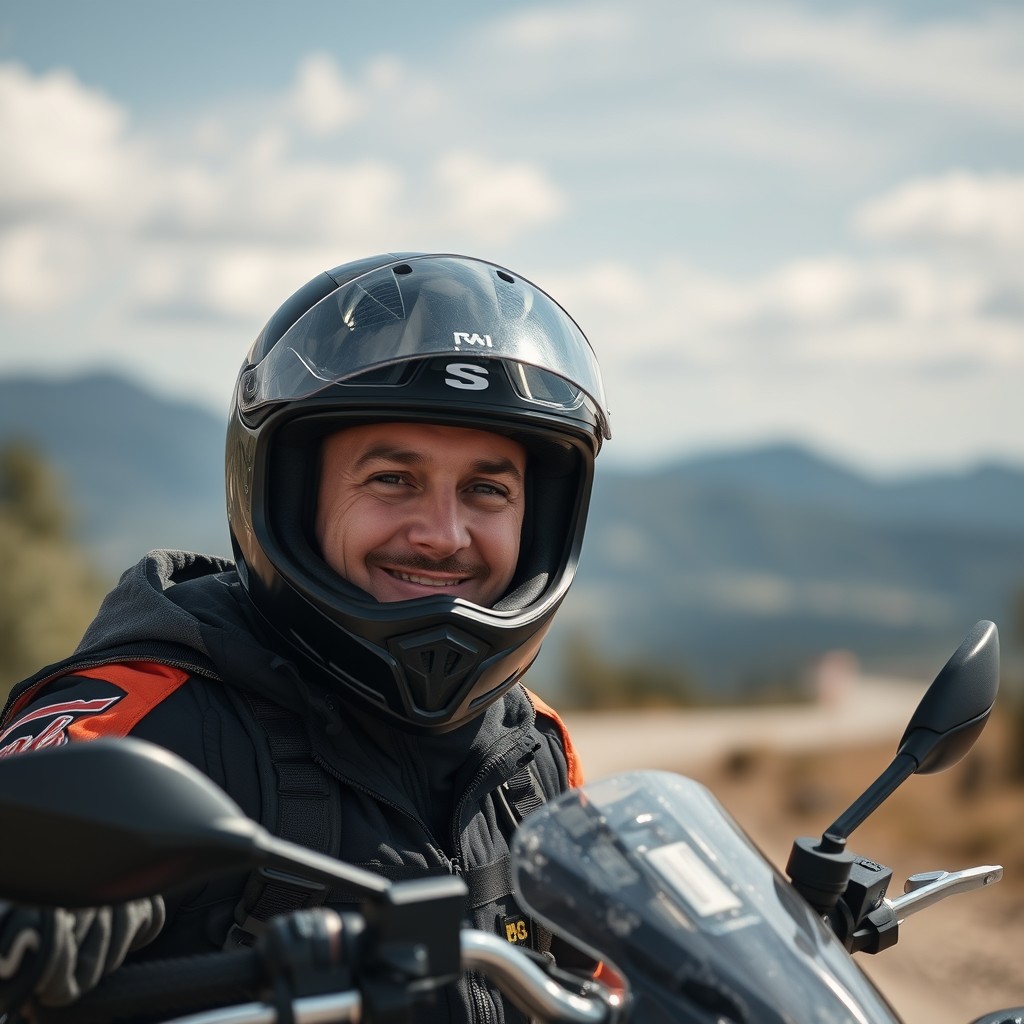
Ryan Thompson is a 35-year-old sport bike enthusiast known for his adventurous spirit. With years of weekend rides and exploring new roads, Ryan brings fresh insights and firsthand experience to ProtectiveGearz. His energetic approach and passion for the latest gear make him a trusted source for riders seeking up-to-date advice.